1. Viskoossuse katse: Viskoossuse hindamine.
Testimise eesmärk:
Viskoossus on HPMC üks olulisemaid omadusi plaadiliimide koostises. See mõjutab otseselt liimi voolavust ja konsistentsi. Õige viskoossus tagab lihtsa pealekandmise, suurepärase liimimise ja kontrollitud avatud aja paigaldamise ajal.

Testimise metoodika:
HPMC-lahuste viskoossust saab mõõta Brookfieldi viskosimeetriga või pöörleva viskosimeetriga. Proov lahustatakse vees nõutava kontsentratsiooniga (tavaliselt 2% massiprotsenti) ja seda katsetatakse kontrollitud temperatuuril (tavaliselt 20 °C). Viskoossus registreeritakse erinevate nihkekiiruste juures. Tootjad peaksid võrdlema viskoossuse tulemusi koostisnõuetega, tagades, et see jääb soovitud vahemikku, et saavutada järjepidevus.
2. Niiskusesisaldus: Stabiilsuse ja ladustamiskvaliteedi tagamine
Testimise eesmärk:
HPMC-i niiskusesisaldus mõjutab selle säilitamisstabiilsust ja toimivust. Liigne niiskus võib põhjustada klompimist, lagunemist või lühenenud säilivusaega. Teisest küljest võib liiga väike niiskus mõjutada lahustuvust ja hüdratsioonikiirust.

Testimise metoodika:
Niiskusesisalduse määramiseks kasutatakse gravimeetrilist analüüsi (ahjukuivatus) või niiskusanalüsaatoreid. Proovi kuivatatakse 105 °C juures, kuni see saavutab püsiva kaalu, ja niiskusesisaldus arvutatakse protsendina algkaalust. Ideaalne niiskusesisaldus peaks tavaliselt olema alla 5%, kuigi see võib erineda sõltuvalt konkreetsetest rakendusvajadustest. Näiteks kõrge õhuniiskusega keskkonnas võib olla vajalik madalam niiskusesisaldus.
3. Osakeste suuruse jaotumine: Lahustumise ja homogeensuse mõjutamine
Testimise eesmärk:
HPMC osakeste suurus mõjutab otseselt selle lahustumiskiirust ja lõpliku plaadiliimi konsistentsi. Peenemad osakesed lahustuvad üldiselt kiiremini ja ühtlasemalt, mis toob kaasa parema dispergatsiooni ja suurema paksendava mõju.

Testimise metoodika:
Osakeste suurusjaotust mõõdetakse tavaliselt laserdifraktsiooni või sõelanalüüsi abil. Need meetodid aitavad määrata proovi osakeste suuruse ühtlikkust. Tootjad peaksid tagama, et osakeste suurusjaotus on optimeeritud, et tagada tõhus segunemine ja ühtlane toimivus lõplikus liimirakenduses. Näiteks eelistatakse sageli osakeste suuruse vahemikku 80-120 võrgusilma, et tagada kiire lahustumine.
4. Lahustuvuskatse: Kiire ja täielik lahustumine
Testimise eesmärk:
HPMC peab tõhusalt ja põhjalikult vees lahustuma, et toimida tõhusa paksendajana. Halb lahustuvus võib põhjustada ebaühtlast dispergeerumist, mis toob kaasa ebajärjekindluse plaadiliimil.

Testimise metoodika:
Standardne lahustuvuskatse hõlmab HPMC-proovi lahustamist soojas vees (40-50 °C) ning lahustumise kiiruse ja lahuse selguse jälgimist. HPMC peaks lahustuma kiiresti, ilma et see moodustaks tükke või jätaks lahustumata osakesi. Selged lahused viitavad kvaliteetsele HPMC-le, mis toimib hästi plaadiliimide koostises.

LANDERCOLL kõrge kvaliteediga HPMC kemikaalid
Hangi HPMC proovid tasuta
Arvestades kvaliteetset HPMC proovid võrdluseks? Võtke nüüd ühendust Landercolliga, et saada oma kohandatud HPMC-lahendusi ja tõsta oma toodete kvaliteeti.
5. Tuhasisaldus: Puhtuse ja kvaliteedi kinnitamine
Testimise eesmärk:
The tuhasus HPMC kujutab endast proovis olevate anorgaaniliste lisandite taset. Kõrge tuhasus võib kahjustada lõpptoote kvaliteeti ja stabiilsust, mõjutades liimi toimivust.
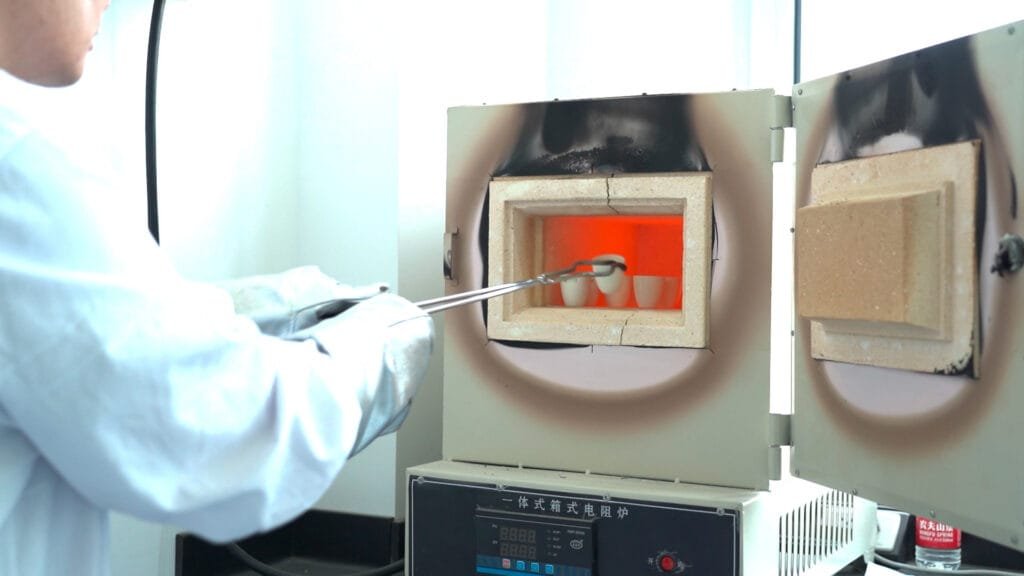
Testimise metoodika:
Tuhasisalduse mõõtmiseks põletatakse proovi kõrgel temperatuuril (600-800 °C), jättes järele anorgaanilise jäägi. Tuhaprotsent arvutatakse järelejäänud jäägi massi alusel. Ideaalis peaks tuhasus olema alla 5%, et tagada kõrge puhtus ja toote stabiilsus. Mõnes piirkonnas, näiteks Euroopas, võib tuhasus olla alla 3%, et vastata kohalikele standarditele.
6. pH väärtus: Toote stabiilsuse tagamine
Testimise eesmärk:
The pH HPMC-lahus mõjutab plaadiliimide stabiilsust ja käitumist, eriti kõvenemise ajal. Vale pH võib põhjustada enneaegset geelistumist või liimi sidemete nõrgenemist.

Testimise metoodika:
Pärast HPMC lahustamist vees mõõdetakse pH väärtust pH-meetri abil. pH peaks tavaliselt jääma 6 ja 8 vahele, mis tagab, et liim jääb stabiilseks ja toimib plaatidega tõhusalt. Näiteks pH 7 on sageli ideaalne neutraalsete rakenduste jaoks.
7. Hüdratsiooniaeg: tootmise tõhususe parandamine
Testimise eesmärk:
Hüdratsiooniaeg viitab ajale, mis kulub HPMC täielikuks lahustumiseks ja dispergeerumiseks vees. Kiire hüdreerumine on tootmise tõhususe seisukohalt väga oluline, sest see tagab kiirema segamise ja plaadiliimide formuleerimise.

Testimise metoodika:
Segage HPMC-proov veega ja jälgige, kui palju aega kulub täieliku hüdreerumise ja ühtlase dispergeerumise saavutamiseks. Ideaalne hüdratatsiooniaeg peaks olema lühike (tavaliselt alla 10 minuti), et parandada segamisprotsessi üldist kiirust, mis tagab tõhusa tootmise.
8. Termiline stabiilsus: Pikaajalise jõudluse tagamine
Testimise eesmärk:
Plaadiliimid võivad nii pealekandmise kui ka kõvenemise ajal kokku puutuda erinevate temperatuuridega. Termiline stabiilsus HPMC tagab, et see säilitab oma omadused kuumuse all ning ei lagune ega kaota viskoossust.

Testimise metoodika:
HPMC proovi tuleb kontrollitud keskkonnas kõrge temperatuuri all hoida ja jälgida selle muutusi. viskoossus või füüsiline välimus. Kvaliteetne HPMC peaks lagunema minimaalselt temperatuuridel, mis esinevad tavaliselt plaadiliimi kasutamisel.
9. Keemilise koostise analüüs: Tooraine terviklikkuse kontrollimine
Testimise eesmärk:
Mõistmine keemiline koostis HPMC tagab, et see vastab plaadiliimide spetsiifilistele funktsionaalsetele nõuetele, kinnitades materjali kvaliteedi järjepidevust ja selle sobivust ettenähtud kasutusviisiks.

Testimise metoodika:
HPMC keemilise struktuuri analüüsimiseks võib kasutada täiustatud meetodeid, nagu infrapunaspektroskoopia (FTIR) või gaasikromatograafia (GC). FTIR on eriti kasulik funktsionaalsete rühmade tuvastamiseks, samas kui GC võimaldab tuvastada lenduvaid lisandeid. Need meetodid annavad teavet materjali puhtuse, funktsionaalsete rühmade ja võimalike saasteainete kohta.
Kvaliteedi tagamine tervikliku HPMC-testimise abil
Sest plaadiliim tootjad, mõjutab tooraine kvaliteet otseselt lõpptoote jõudlust ja vastupidavust. HPMC-proovide testimine põhiparameetrite - viskoossuse, niiskusesisalduse, osakeste suuruse, lahustuvuse, tuhasuse, pH väärtuse, hüdratatsiooniaja, termilise stabiilsuse ja keemilise koostise - suhtes annab kriitilisi andmeid, et tagada lisaainete vastavus koostise spetsifikatsioonidele.
Põhjalikult testides HPMC, saavad tootjad optimeerida oma tootmisprotsesse, vähendada varieeruvust ning parandada plaadiliimide järjepidevust ja kvaliteeti. Need testid ei paranda mitte ainult toote jõudlust, vaid aitavad ka säilitada klientide rahulolu, tagades iga partii puhul usaldusväärsed ja kvaliteetsed liimid.
Järgides neid rangeid testimisprotokolle, võivad tootjad kindlalt kasutada HPMC-d plaadiliimides, teades, et nad parandavad nii toote kvaliteeti kui ka jõudlust.
Landercoll: HPMC-testimine ja kohandatud lahendused
Tootjate toetamine kvaliteedi tagamisega
Veebilehel Landercollme mõistame, kui oluline on tagada, et iga koostisosa teie plaadiliimi koostises vastab kõrgeimatele standarditele. Seepärast läheme me kaugemale HPMC pakkumisest; me pakume järgmist põhjalikud testimisteenused tagamaks, et meie tooted on püsivalt tõhusad ja vastavad teie spetsiifilistele koostamisnõuetele. Meie tipptasemel laboratoorsed uurimisvõimalused on varustatud kõigi eespool kirjeldatud oluliste katsete läbiviimiseks, alates viskoossusest kuni termilise stabiilsuseni.
Teie vajadustele kohandatud testimine
Meie pühendumus kvaliteedile laieneb personaalsele toetusele kogu tootmisprotsessi jooksul. Enne iga saadetise väljumist meie rajatisest testime HPMC-proovide põhjalikult, et tagada nende vastavus teie poolt nõutavatele spetsifikatsioonidele ja toimivusnormidele. Kui teil on vaja kohandatud viskoossust, lahustuvuse kohandamist või muid koostisega seotud kaalutlusi, saab meie laboratoorium muuta toodet vastavalt teie vajadustele, aidates teil saavutada soovitud tulemusi teie plaadiliimide tootmisel.
Miks valida Landercoll HPMC?
- Põhjalik testimine:Me testime HPMC-proovide viskoossust, niiskusesisaldust, lahustuvust ja muud, et tagada nende vastavus tööstusstandarditele.
- Individuaalsed lahendused:Meie laboris kohandatakse HPMC vastavalt teie konkreetsetele rakendusnõuetele, et tagada optimaalne liimi jõudlus.
- Usaldusväärsed tulemused:Tänu rangele tarnimiseelsele testimisele võite olla kindel, et teie saadud HPMC vastab iga kord täpselt teie vajadustele.
- Ekspertide juhised:Meie tehniline meeskond on valmis teid toetama retseptuuri kohandamisel, aidates teil saavutada paremaid plaatliimitooted.
Kvaliteet, mida võite usaldada plaatide liimi tootmises
Landercolli kõikehõlmavad testimisteenused annavad täiendava kindluse, et teie plaadiliimide koostised toimivad ootuspäraselt. Tehes tihedat koostööd meie laboratooriumiga, saate juurdepääsu kohandatud lahendustele, mis aitavad teil täita klientide nõudmisi ja tagada toote kvaliteedi igas tootmisetapis. Landercolli HPMC-ga ei saa te mitte ainult tipptasemel materjale, vaid ka ekspertteadmisi ja tuge erakordsete plaadiliimide loomiseks.


